The TI 980 system is capable of extremely rapid testing, called Accelerated Mechanical Property Mapping, or XPM. This testing mode allows for hundreds of indents to be made in a matter of minutes. A property map can be made from the indentation data, allowing for identification of different regions or phases within a tested material. Several XPM tests can also be performed in a larger array and stitched together in one large property map. Further data analysis can be done through an analysis program called TriboIQ to eliminate outliers and do statistical analysis of specific regions on the map.
Typical Experimental Results
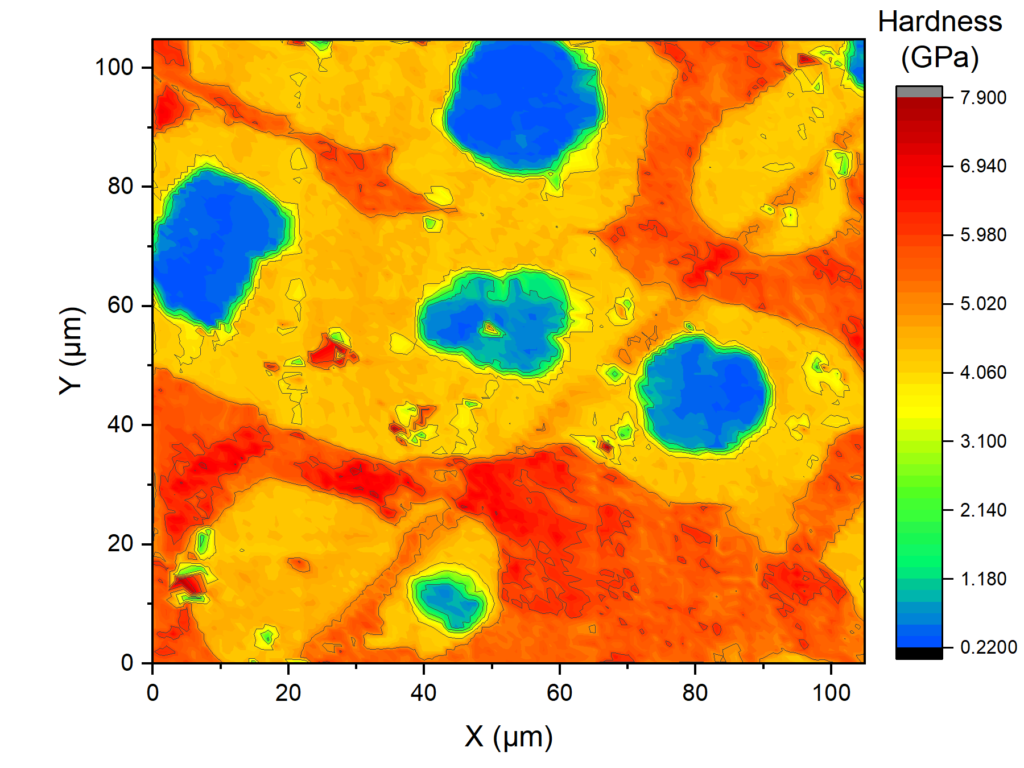
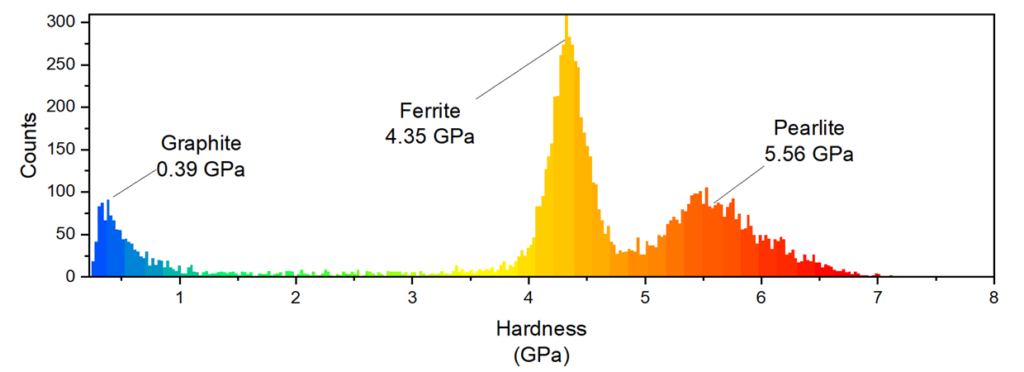
Applications
Aggregates | Ceramics | Composites | Medical Devices |
MEMS devices | Metal Alloys | Multiphase Materials | Polymer Fillers |
Property Mapping | Semiconductors | Thin Films | Metal Interfaces |
For more information, please read our application notes:
Accelerated Nanomechanical Property Mapping of Ductile Cast Iron
Instrument: Bruker Hysitron TI 980
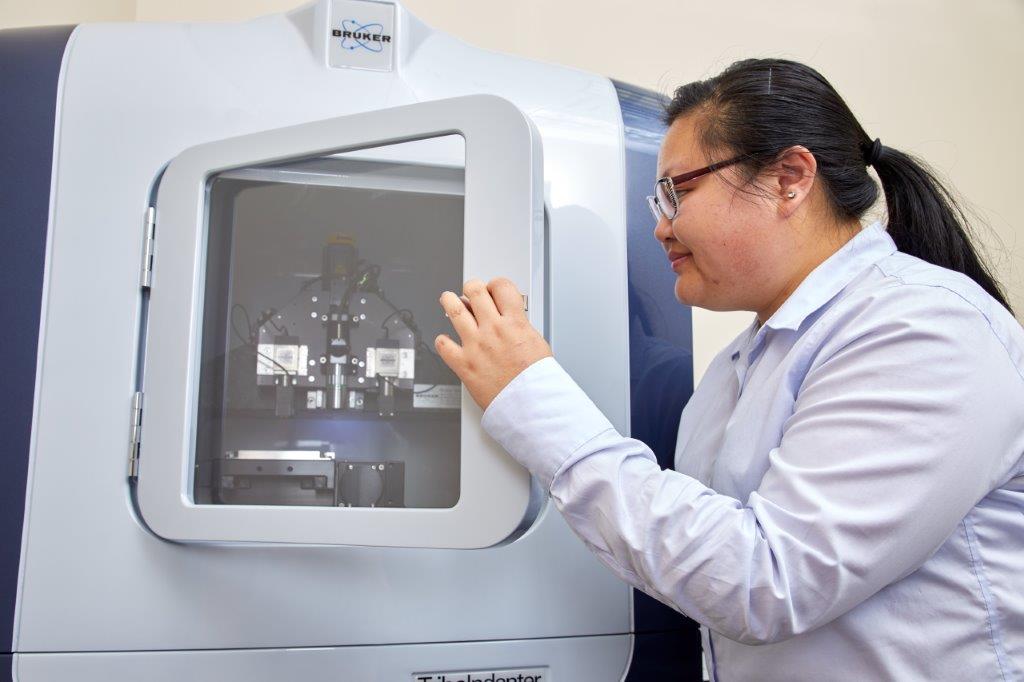

Key Specifications
Modulus Precision | ± 1% |
Displacement Range | 15 μm |
Displacement Resolution | 0.02 nm |
Force Range | 30 nN to 10 mN |
Force Resolution | 1 nN |
Atmosphere | Open Air, Inert Gas |
Accelerated Nanomechanical Property Mapping of Ductile Cast Iron
The mechanical properties of a material are some of the most important considerations in the design of a part. Bulk mechanical properties can easily be measured using macroscale methods such as tensile testing, compression testing, or indentation. However, many important materials such as alloys, plastics, or ceramics frequently contain multiple phases in the forms of fillers, inclusions, precipitates, secondary phases, or impurities. In order to understand and predict mechanical performance of multiphase materials, it is critical to determine the mechanical properties of each phase at the nano- and microscale.
Nanoindentation is a well-established method for measuring mechanical properties at the nanoscale by measuring the displacements of a calibrated indenter tip into a specimen’s surface while forces are being applied. The force versus displacement curve is used to obtain the material’s elastic modulus and hardness based on the Oliver and Pharr method. Since the interaction volume between the indenter tip and the material is small, nanoindentation can reach nanometer spatial resolution. Traditional quasi-static nanoindentation takes days of work to obtain the large numbers of measurements needed for mapping a sizeable area containing multiple phases. Recent advancements in nanoindentation techniques have significantly reduced the testing time required and a similar mechanical property map can be obtained in a matter of hours.
Ductile cast iron is a multiphase material that is well known for its superior vibration dampening capability and wear resistance. These properties are directly related to its multiphase microstructure. To better understand the individual phases’ contribution to the bulk properties, express nanoindentation property mapping was used to obtain high resolution mechanical property maps of 5560 ductile cast iron. This type of cast iron contains spherical graphite nodules embedded in a matrix of ferrite and pearlite. A Bruker TriboIndenter TI 980 with accelerated mechanical property mapping (XPM) was employed in this study. 10,000 indents spanning 106 × 106 μm2 and spaced 1μm apart were made at a rate of 0.3 seconds per indent.
Figure 1. Nanohardness map (top) and histogram (bottom) of 5560 ductile cast iron; hardness represented in color; median hardness values for each phase noted on the histogram.
Figure 1 shows the hardness map determined from the XPM test. Different colors represent different hardness values. Figure 1 clearly shows that three distinct phases with different nanohardness values are present. The yellow-colored ferrite phase surrounds each blue-colored graphite nodule while the harder, red-colored pearlite phase makes up the rest of the matrix. Green colored regions represent the transition between the graphite nodule to the ferrite. Interestingly, a diagonal line of slightly higher hardness indicates a scratch where the material was probably work hardened.
Figure 2. Reduced elastic modulus map of 5560 ductile iron with graphite nodules measured using nanoindentation.
Figure 2 is an elastic modulus map of the same area as shown in Figure 1. As can be seen from Figure 2, the blue-colored circular regions are low-modulus graphite nodules, while the orange-colored regions are ferrite and pearlite. Their color difference is small due to their similar elastic moduli.
Figure 1 (bottom) presents the histogram of the hardness data. The three peaks in the histogram correspond to the graphite, ferrite, and pearlite phases in the specimen. Multivariate cluster analysis enables the determination of the average hardness and modulus for multiple phases, even when two phases have similar modulus values, as shown in Table 1.
Table 1 Average Nanohardness and Elastic Modulus of Individual Phases Determined using XPM and Cluster Analysis
Phase
Nanohardness (GPa)
Reduced Elastic Modulus (GPa)
Graphite
0.73 ± 0.55
33.6 ± 24.28
Ferrite
4.31 ± 0.35
197.47 ± 19.71
Pearlite
5.68 ± 0.53
205.84 ± 13.30
As demonstrated in this application note, the express nanoindentation mapping technique can survey nanomechanical properties at impressive speeds. The map not only provides statistically significant results for individual phases, but also visualizes their high-resolution spatial distributions. It also offers unprecedented insight into the understanding of multiphase materials.